A marble processing factory in Namibia — modeled using UL Solutions HOMER® Pro and designed to operate off the grid — is running reliably on a microgrid and saving what would have been significant grid energy costs. Additionally, plans are underway to expand the factory.
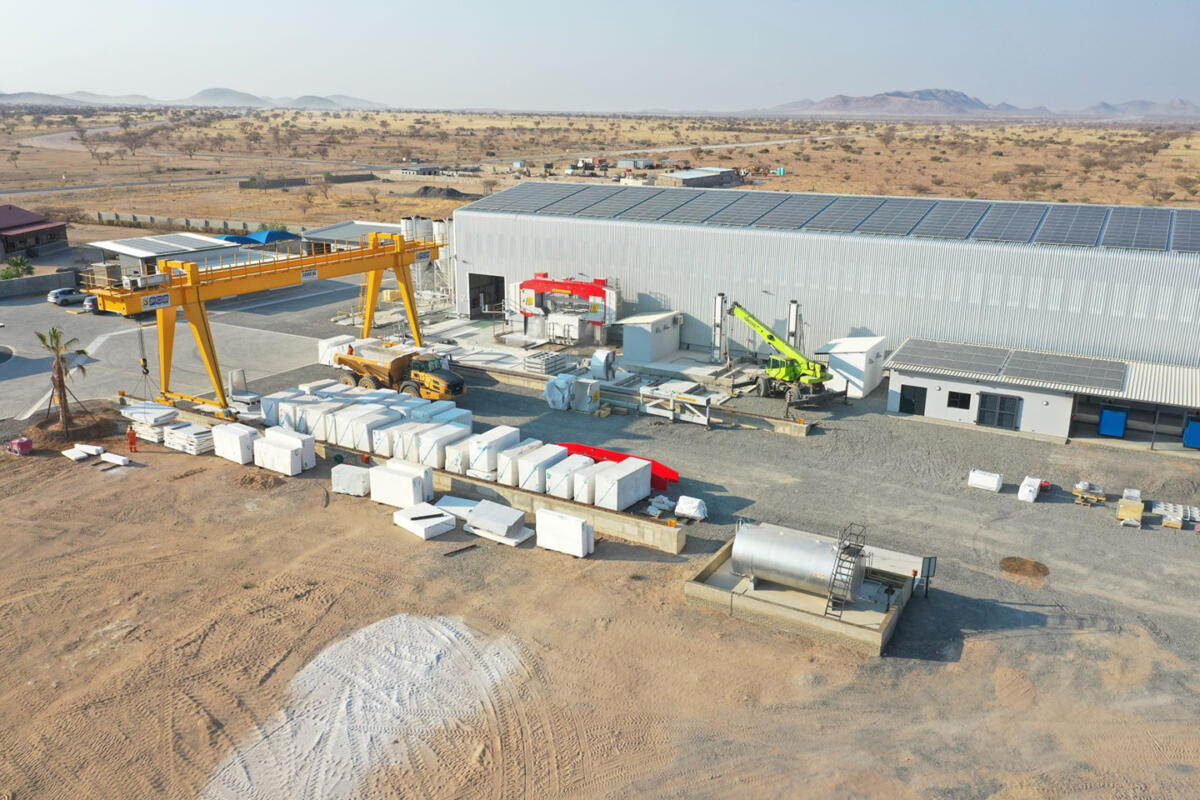
Growing consumer demand for decorative and architectural stone provides opportunities and challenges in Namibia, which has substantial deposits of white marble and a growing export industry based on “dimension” stone. Dimension is the industry term for stone quarried in large blocks, then cut into slabs or specific sizes for sale in real estate, interior design or artistic projects.
According to Glenn Howard, an engineer and founder of Shawapala Consulting, burgeoning marble exports led a family-owned Namibian business to ask him to design the electrical services for a new factory to process the white marble. While the family requested the company name be kept private, Howard has permission to disclose details of the steps he took to design and build the factory and its hybrid power system. The power system exceeded economic expectations in the first 18 months of operation.
Howard was trained as a mechanical engineer and describes himself as an engineering “jack of all trades” — a building services engineer whose varied experience in energy efficiency and renewable energy gives him an advantage in hybrid power system design. A user of HOMER software for many years, Howard said he learned how to build off-grid microgrids through his work designing remote tourist lodges that enable travelers to get closeup views of African wildlife.
The stone factory project grew from a relationship with the owner, who had engaged Howard to design his home’s mechanical and electrical services, including solar and hydronic heating systems. Previously, the owner had another stone factory, which he decommissioned before selling. However, even after the factory’s operations ceased, the local utility continued to bill for expensive monthly fixed costs. When the owner decided to build a new state-of-the-art factory, he was adamant it would be independent of the utility.
A Namibian stone factory’s energy needs
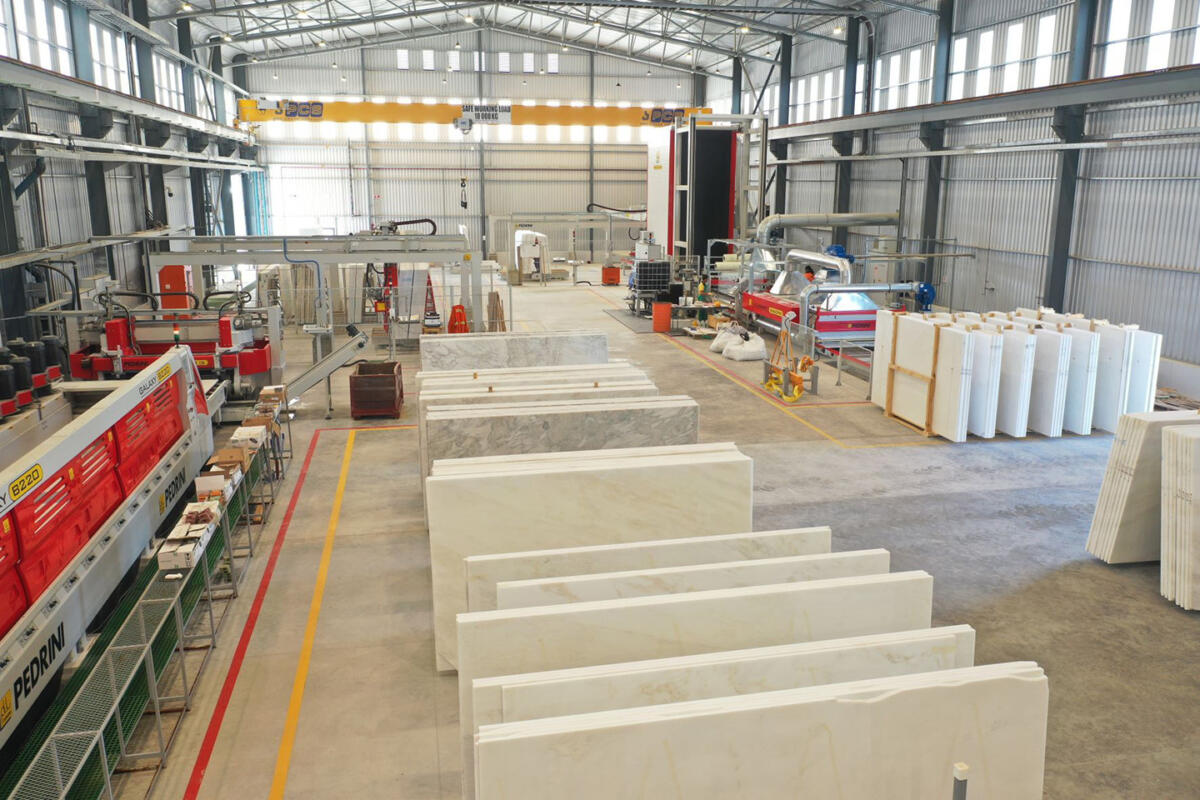
Howard explained that the processes used at a stone factory are energy-intensive, creating a peak factory load of around 700 kilowatts (kW). First, miners cut large blocks of marble at the quarry, then transport them to a factory where diamond-encrusted wires cut them into one-inch slabs. Marble is relatively soft and porous, so the stone must first be treated for uses like kitchen countertops. In that process, special ovens seal marble slabs with high-heat resins. Then the slabs are transferred to polishing machines.
Howard’s optimal system design includes a 350-kW solar photovoltaic (PV) system and two 400-kilovolt-ampere (kVA) generators to keep the stone-processing operation running smoothly. The grid-forming generators play an essential role in integrating electricity from the solar system into the microgrid, so they run whenever power is needed. With a load that large, batteries would have been prohibitively expensive and, at the time, still uneconomic, Howard explained.
Based on experience from other feasibility studies, Howard suspected that grid electricity might be more expensive than self-generation when he began designing the factory system, but he wasn’t sure how much more costly it would be. He modeled the system with HOMER Pro to determine the economics, including a simulation of grid-only power costs and a grid-tied solar PV system. The model predicted that although the off-grid solar-plus-diesel system had the highest capital cost, it would have the best rate of return over 10 years.
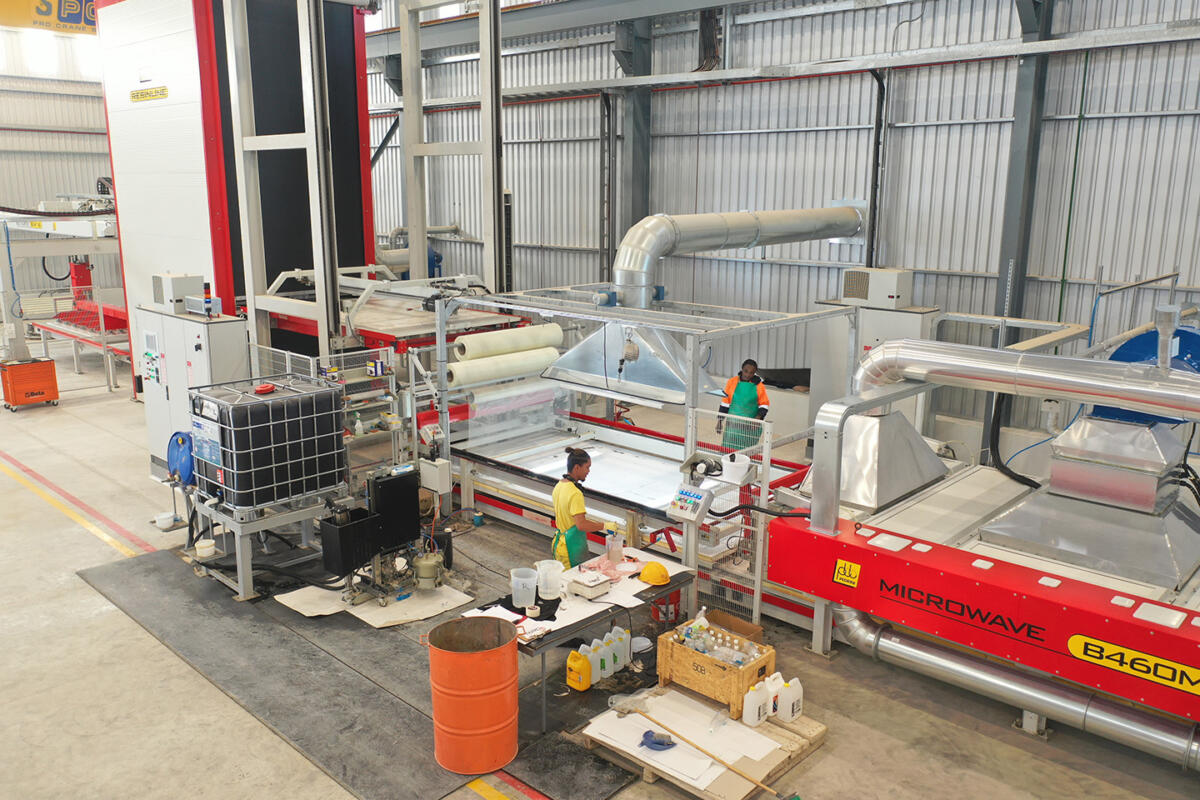
“It’s very tricky to estimate the load profile for a factory,” Howard said. “It’s easier for us to predict the load profile of a residence since there is lots of research data, but there are many more unknowns in factories.”
The HOMER Pro model showed that the off-grid energy would cost 63% of grid power, but the reality turned out to be a much lower 48%.
As is often the case, the discrepancy between the model and reality stemmed from inaccurate load data. When Howard began his HOMER Pro modeling, the factory building did not exist. “It was basically a shed with sophisticated machines in it,” Howard stated. “The machine manufacturers overstated the load requirements, so we used less energy than we had anticipated. So, HOMER wasn’t wrong; people were.”
The capital costs were also lower than expected because the owners were able to get an excellent deal on solar components. That has allowed the factory to implement two extensions without requiring changes to the power system. For example, Howard subsequently designed a phytosanitary treatment plant for the company to fumigate the timber used for shipping marble slabs. The timber treatment qualifies the wood as insect-resistant and allows the company to ship its pallets to the United States and Europe legally. The off-grid system also powers the treatment plant, which has cut the cost of packaging timber in half.
Howard also used HOMER Pro in a separate project at the same location to model the system that powers essential services in an office building, such as security, lighting and a computer network. That system has 16 kW of solar and 46 kilowatt hours (kWh) of battery storage.
Finally, SMA Solar Technology AG inverters equipped with their proprietary control systems provide the controls for the microgrid.
Future upgrades are in the works
The owner plans to expand the stone factory to keep up with the increased demand for marble, much of which they now ship to North America. That calls for new machines and other upgrades, factory expansion, and additional solar PV, the exact amount to be determined by more modeling with HOMER Pro. Howard has also designed upgrades for recycled water distribution, compressed air, and power distribution systems, which will require more electricity to operate.
An off-grid system in Namibia can provide more reliable power than the grid
Howard explained that, ironically, going off the grid in Namibia reduces the risk of being without power. Namibia gets about 60% of its energy from South Africa, primarily from an aging fleet of coal-fired power plants. Because of economic and management issues with these plants, the South African utility Eskom has now implemented an aggressive schedule of load shedding, or rolling blackouts. In some cities, such as Cape Town, residents can be without power for as much as 10 hours daily, creating massive business challenges, according to a news report from Reuters.
Fortunately, according to Howard, Namibia has not had to implement the kinds of planned blackouts that could cause serious economic disruption. Still, he worries that if South Africa’s power utility stumbles, Namibia will catch the regional contagion of load shedding.
Howard said that a loss of power could destroy an entire stone production run, resulting in significant financial loss. He added that considering the electrical independence and cost-savings the microgrid-powered stone factory has gained, an off-grid system in Namibia is an attractive business proposition and effective risk-reduction strategy.
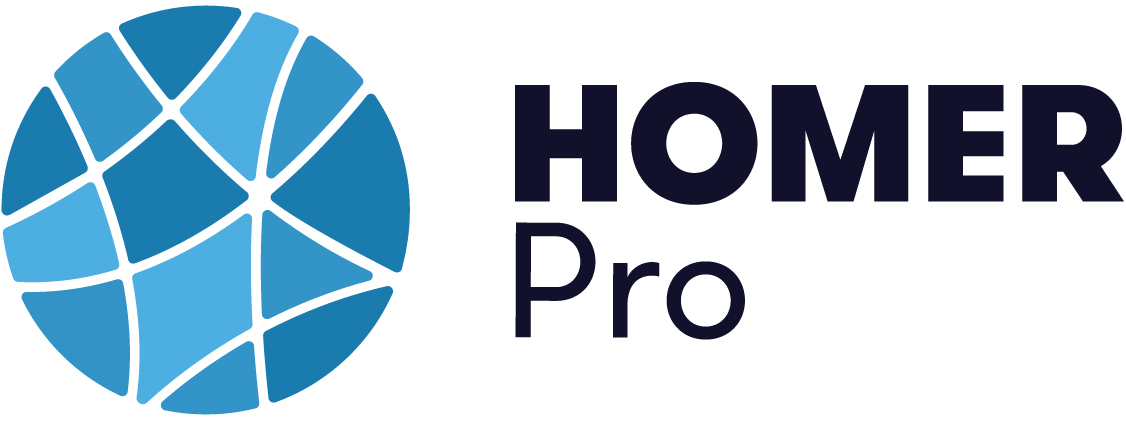
UL Solutions’ HOMER® Pro is the leading pre-feasibility design software for modeling microgrids, with more than 250,000 users in more than 190 countries. It provides engineering and financial analyses of remote, off-grid and grid-tied complex distributed energy systems, helping reduce financial risk for owners and developers. Learn more about HOMER Pro and download a complimentary trial.